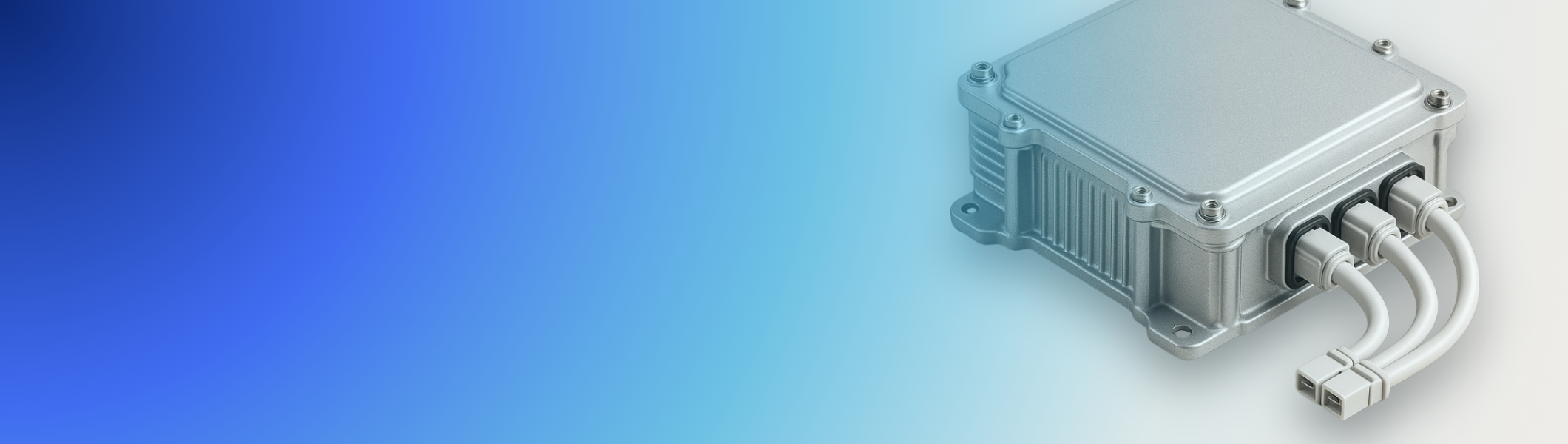
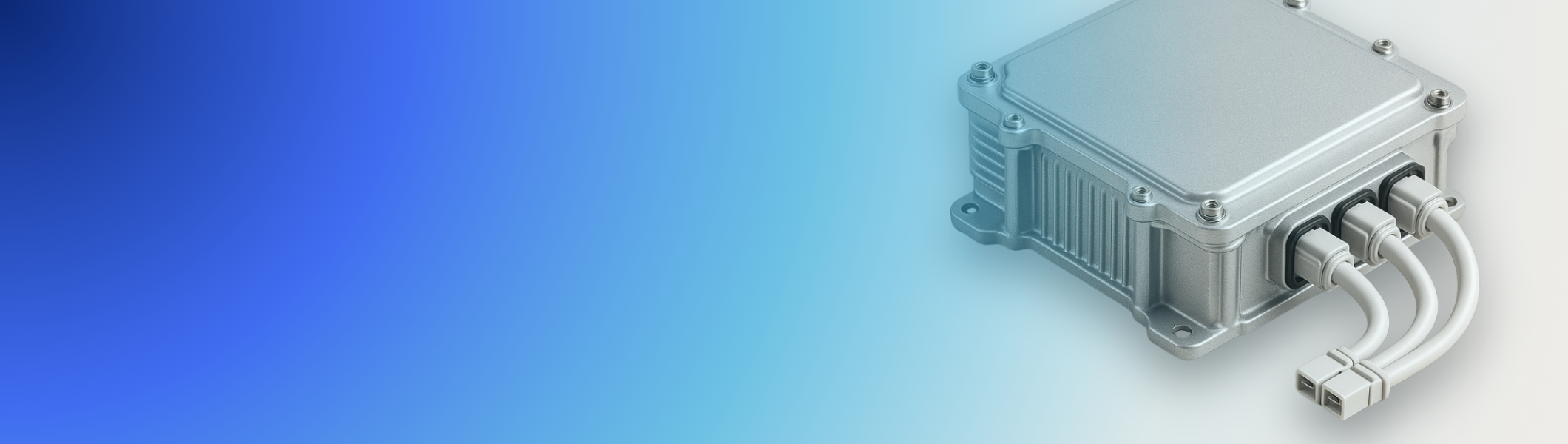
This blog is part of a spotlight series showcasing real-life case studies of OEMs who were able to utilize their connected vehicle data, powered by ML and AI to detect component failures earlier, reduce warranty costs, and improve customer satisfaction at scale.
Each case highlights how Upstream’s Proactive Quality Detection (PQD) solution helps OEMs to accelerate root-cause analysis (RCA), severity assessment, and prioritization of vehicle quality issues using AI-driven insights.
A Small Number of Complaints, Hiding a High-Severity Component Failure
In a specific EV model, a North American OEM began receiving a small number of complaints reporting sudden drops in propulsion during acceleration. Drivers described brief but sharp slowdowns, typically accompanied by the powertrain fault warning or “Check Engine” light.
Diagnostics revealed a recurring “Drive Motor A Current Fault” Diagnostic Trouble Code (DTC), and in several cases, inverter temperatures spiked beyond 90°C (194°F), far exceeding the typical 25°C (77°F) to 50°C (122°F) range. Yet despite these warning signs, the issue appeared sporadic and difficult to reproduce. In many cases, the fault cleared itself temporarily, and standard service actions like cooling system flushes or pump replacements failed to address the root cause.
From the dealership’s perspective, there was no clear failure pattern. And while the number of affected vehicles was small, the safety implications were significant: loss of propulsion at speed, thermal stress on high-voltage components, and potential risk of thermal events.
This was exactly the kind of scenario that traditional recall triggers, rule-based systems, and static thresholds are not equipped to handle, especially when faults are intermittent, condition-dependent, and buried deep in noisy data.
Illustration: Inverter, EV (Source: Upstream)
Shifting to a Proactive Quality Approach, Before Claims Escalate
Rather than waiting for the pattern to grow, the OEM’s after-sales team leveraged Upstream’s PQD platform. Unlike conventional analytics dashboards or diagnostics logs, PQD uses a cloud-based, agentless approach to continuously ingest, normalize, and contextualize connected vehicle data, from telematics, DTCs, ADAS systems, EV components, and more.
Utilizing Upstream’s mobility live digital twin, the platform created a digital representation of fleet-wide behavior to establish baselines. It then used AI and ML-based analytics to detect anomalous behaviors at scale.
PQD identified a “torque loss signature”: actual motor output was consistently and abnormally low compared to expected values based on driver pedal input, especially under high load conditions. These anomalies consistently aligned with abnormal inverter temperature spikes.
AI-Driven RCA Correlated Telemetry, DTCs, and Real-World Conditions
What made this detection possible wasn’t just pattern recognition, it was contextual correlation. PQD cross-referenced live telemetry streams, DTCs, vehicle metadata, as well as live usage signals and patterns to build a complete picture.
This allowed the platform to separate signal from noise, uncovering that the actual root cause was an intermittent electrical fault in the inverter’s internal power supply, not a thermal system failure as previously suspected. The faulty connection intermittently disrupted torque delivery to the drive motor and caused thermal overloading during acceleration.
Armed with this insight, the OEM was able to:
- Confirm root cause without waiting for broader claim volumes
- Implement targeted counter measure (inverter unit replacement and thermal validation)
- Reduce unnecessary part replacements, repeated service visits, and diagnostic churn
- Apply detection logic across similar vehicle lines, boosting fleet resilience
Upstream’s Proactive Quality Detection Platform
This inverter fault didn’t raise red flags through traditional channels. It was subtle, intermittent, and initially rare. But it posed serious risks. What changed the trajectory was Upstream PQD’s ability to detect the anomaly early, trace the root cause, and guide corrective action, all before reputational damage or large-scale exposure.
For OEMs navigating the complexity of EVs, software-defined architectures, and global fleets, the stakes are only rising. Quality leaders need tools that can see around corners. Upstream PQD enables this through data, AI, and context.
Explore Upstream’s PQD platform to see how early quality issue detection and contextual analysis can support faster RCA, reduce warranty exposure, and improve customer satisfaction.
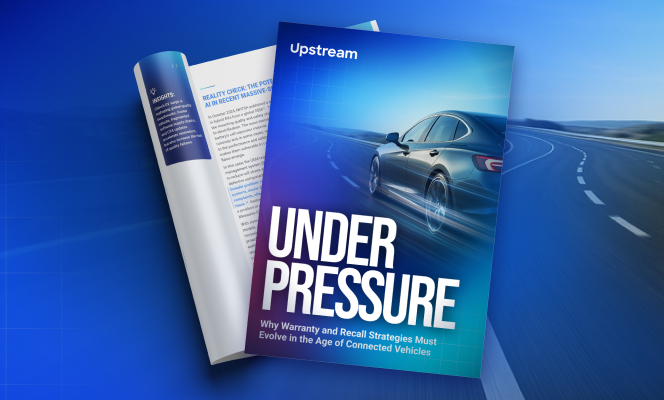